Sheet metal bending is a critical process in metal manufacturing and vital in manufacturing industries such as automobiles, aerospace, and hardware. Manufacturers often turn to CNC (computer numerical control) machines to achieve precision and efficiency in sheet metal bending. Choosing the suitable CNC metal bending machine ensures high-quality output and minimizes production costs. In this ultimate blog, we’ll explore the key factors to consider when selecting the best CNC metal bending machine for your specific needs.
Learn about sheet metal bending.
Before delving into the intricacies of CNC metal bending machines, it is necessary to have a deep understanding of sheet metal bending. This process applies pressure to the metal sheet, causing it to bend and deform under the action of the bending die, thereby achieving the processing and shaping of the metal sheet. Many factors affect the sheet metal bending process, including material thickness, bending radius, and the type of material used. Achieving precise and repeatable bends is critical, and this is where CNC machines come into play.
Key factors to consider when choosing a CNC metal bending machine
1. DAG CNC offers machine types
CNC Press Brake with Upstroke Moving (upstroke type)
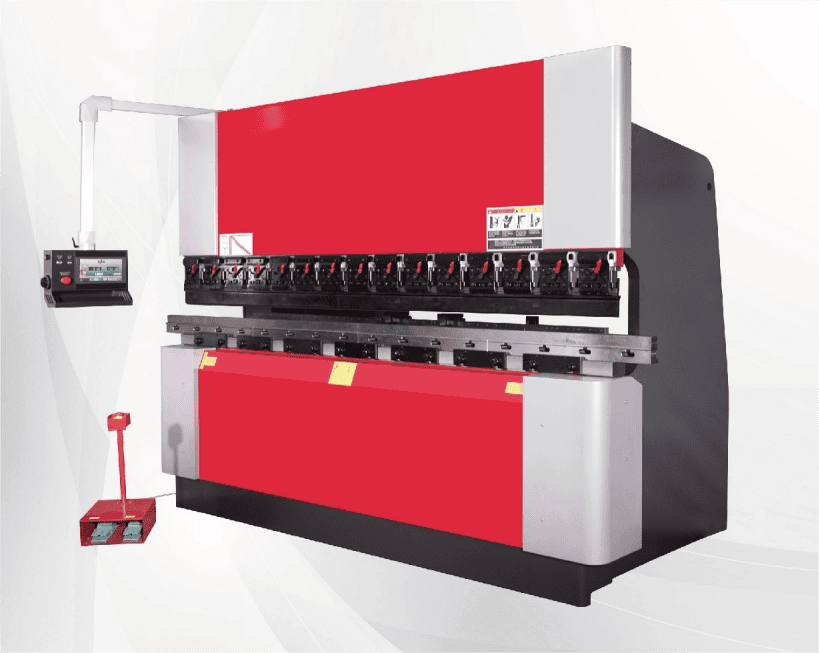
Electro-Hydraulic Servo CNC Press Brake Machine (Down Stroke Type)
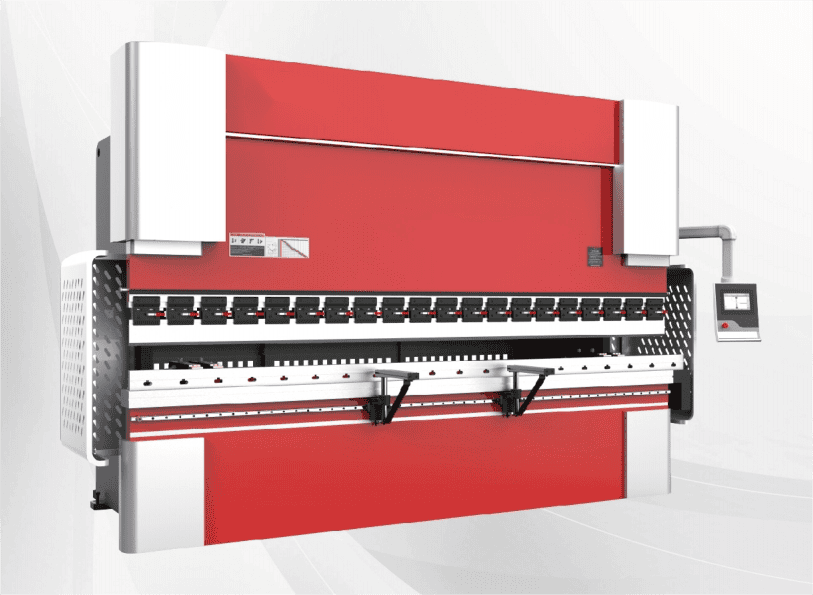
Full Servo Pure Electric Ball Screw CNC Press Brake (Down Stroke Type)
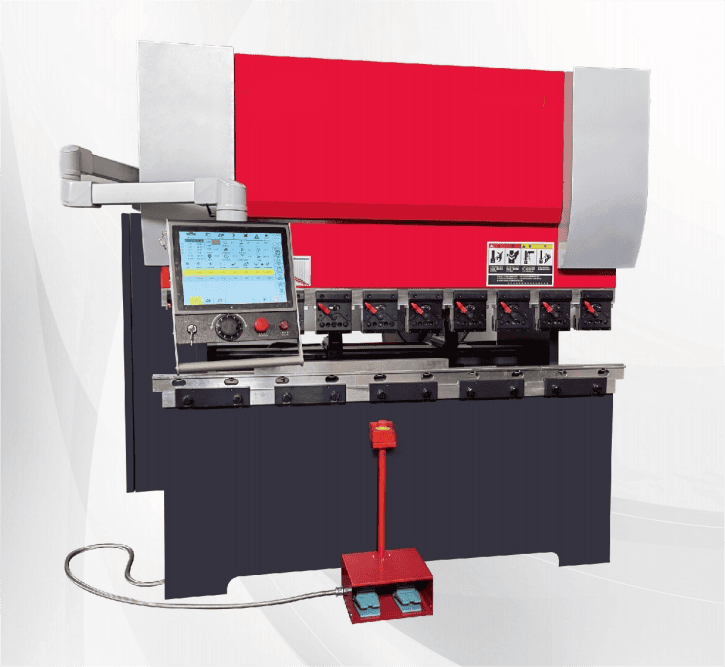
2. Material compatibility
Different sheet metals have different properties, including thickness, hardness, and elasticity. Choosing a CNC metal bending machine compatible with the materials you frequently work with is crucial. Look for a machine that can handle a variety of materials to increase the versatility of your manufacturing projects.
3. Bending ability
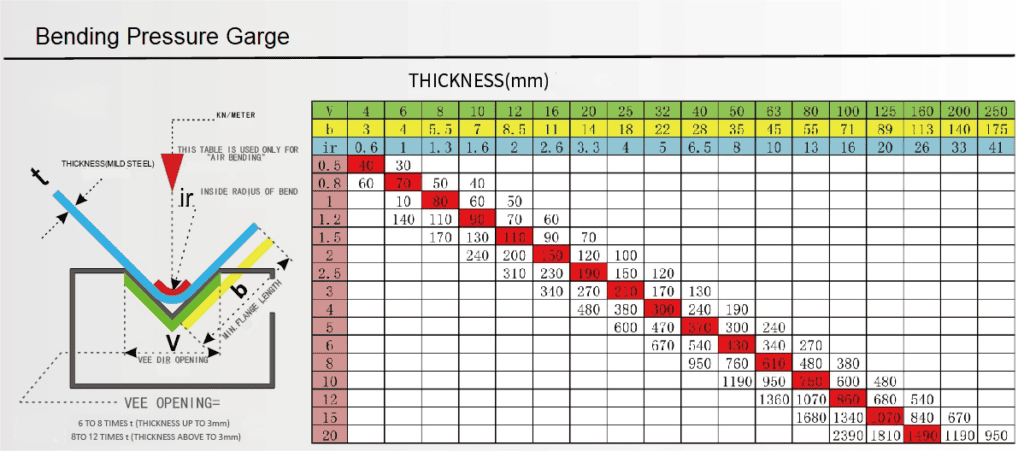
Tonnage
One of the most critical factors is tonnage, which indicates the capabilities of the press brake.
● Traditionally, the thicker or longer the material bent, the higher the tonnage required.
● Softer metals such as aluminum and copper require less tonnage than stainless steel, carbon steel, or other high-strength materials.
● Mold length and die opening width are also important factors. Traditionally, a smaller V shape meant higher tonnage.
● Air bending requires lower tonnage compared to bottom bending and moulding.
It should be noted that when selecting a bending machine, the maximum tonnage should be 20% to 30% higher than the actual required tonnage. This ensures the machine can operate at full load when working under maximum pressure, affecting its service life.
Length
The bending machine’s length depends on the workpiece’s maximum length that needs to be processed. Considering the maximum height it can handle, choosing a machine that matches your usual board sizes is crucial to avoid limitations in manufacturing capabilities.
4. Accuracy and Precision
Precision and consistency are critical to achieving high-quality bends. Look for a CNC metal bending machine that delivers high precision, ensuring the bend is done right the first time. Maintaining this accuracy consistently minimizes the need for extensive post-bending inspection, especially for heavy and bulky workpieces. Features such as advanced control systems and back gauge positioning can improve accuracy, especially when dealing with complex designs or tight tolerances.
5. Easy to use
In today’s press-bending industry, finding professionals can be challenging, and constant employee turnover is a common obstacle. Therefore, choosing a press brake that is easy to operate and has intuitive controls suitable for all experience levels is crucial. This ensures that experienced operators and those new to the industry can use the machine effectively. Additionally, consider the possibility of interconnecting the press brake with the technical department responsible for programming to facilitate a seamless workflow.
6. Ergonomics
The ergonomic design of CNC metal bending machines also plays a vital role in optimizing productivity and reducing the risk of accidents. Look for machines that prioritize user comfort and adaptability. Features like self-aligning pneumatic clamps that can be placed in any position without tools can significantly improve the overall ergonomic experience. Additionally, consider integrating an automatic tool changer to enable frequent machining and complex setups and reduce the handling of heavy and expensive tools.
7. Automation features
Automation can significantly increase productivity and reduce reliance on manual labour. When choosing a CNC metal press brake, consider advanced automation features such as robotic arms for material handling, automatic tool changers, and intuitive programming interfaces. These features streamline production processes and minimize downtime.
8. Programming and Software
Evaluate the programming capabilities and software compatibility of CNC metal bending machines. Ensure the machine’s programming capabilities match your requirements, allowing easy customization and efficient workflow management. Compatibility with industry-standard software tools further enhances machine versatility and integration with existing systems.
9. Tool options
Consider the availability and compatibility of tooling options for your CNC metal bending machine. Tool settings significantly affect the types of bends you can achieve. Improve workflow efficiency by choosing a machine that offers a variety of tooling options and allows for quick and easy tool changes.
10. Maintenance and Support
Choosing a CNC metal bending machine from a reliable manufacturer will ensure you receive comprehensive maintenance and technical support. Evaluate the manufacturer’s record of providing timely assistance, spare parts availability, and regular maintenance services. A reliable support network minimizes machine downtime and optimizes long-term productivity.
11. Cost and Return on Investment (ROI)
While cost is essential, it should not be the only deciding factor in choosing a CNC metal bending machine. Consider the overall return on investment (ROI) by evaluating machine functionality, reliability, and long-term cost savings. In the long run, a higher initial investment in a machine with superior functionality and performance may increase productivity, reduce operating costs, and improve product quality.
12. User reviews and recommendations
Get user reviews and recommendations from industry professionals with first-hand experience with the CNC metal press brake you are considering. Their insights can provide valuable information about machine performance, reliability, and overall customer satisfaction.
In summary, choosing the CNC metal bending machine that best suits your needs requires careful consideration of various factors. By evaluating machine type, material compatibility, bending capabilities, accuracy, ease of use, ergonomics, automation features, programming and software, tool options, maintenance and support, cost and ROI, and user reviews, you can make Smart decisions that maximize the quality and efficiency of your sheet metal bending operations. Remember to prioritize the unique needs of your business and seek guidance from industry experts to ensure the best results.